This website uses cookies so that we can provide you with the best user experience possible. Cookie information is stored in your browser and performs functions such as recognising you when you return to our website and helping our team to understand which sections of the website you find most interesting and useful.
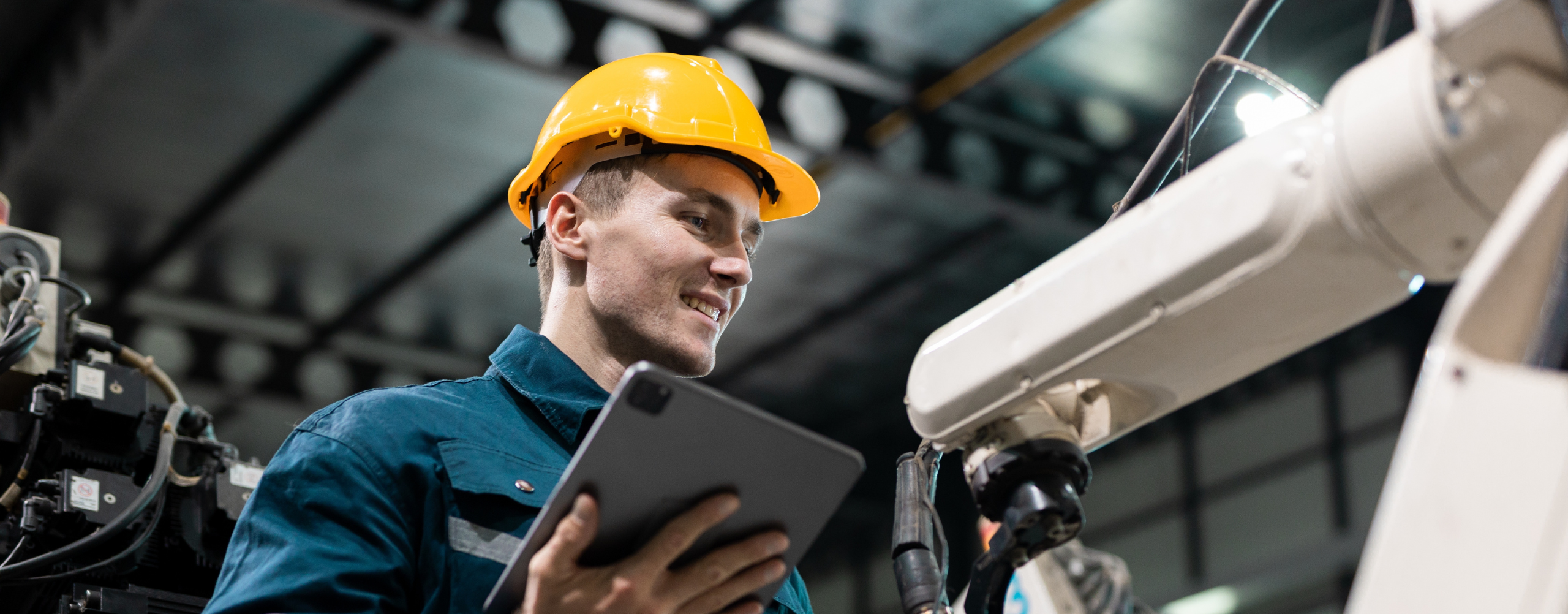
Client
A leading North American manufacturer of metal components. The company operated two types of machines: an advanced but energy-intensive model, and an older one – more affordable to maintain but requiring manual operation.
Challenge
At one of the company’s factories in Toronto, hundreds of metal components were cut daily – ranging from simple shapes to complex designs. The production relied on two machines:
- A modern, fully automated machine that was expensive to run
- An older, more cost-effective machine that required manual parameter setup for every new project
From a cost perspective, using the older machine was significantly more economical (the cost to produce a single part was half as much). However, operating it posed several challenges:
- Hours spent analyzing DXF files and manually configuring settings
- High risk of errors leading to material waste and downtime
- Overuse of the more expensive machine and underutilization of the cheaper one
- Excessive energy consumption and unnecessary operational costs
For four years, the company had unsuccessfully tried to optimize the process of assigning tasks to machines. To effectively cut costs, they needed a solution that would automate this process – enabling the cheaper machine to operate with the same precision and speed as its modern counterpart.
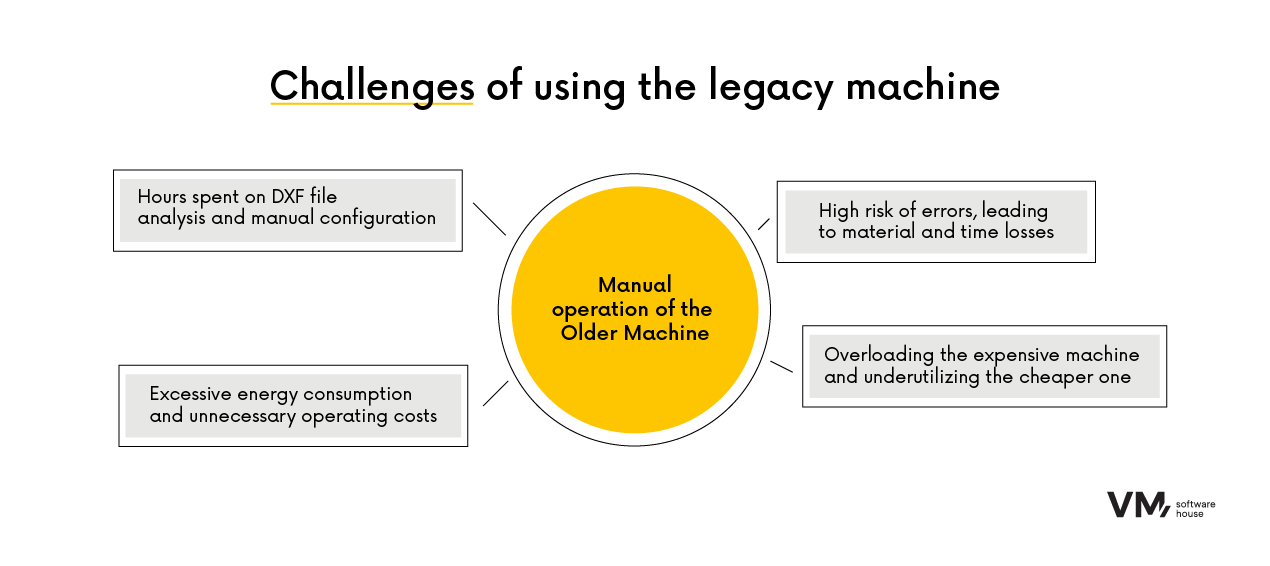
Solution
We designed a machine learning-based system for shape recognition, combined with a rule-based algorithm to assign tasks to the appropriate machines.
How does the system work?
- Monitors production processes
- Automatically analyzes DXF files and identifies the shape of each part
- Checks geometry accuracy
- Generates optimal cutting parameters
- Assigns the task to the appropriate machine – with no manual operator input
We started with an MVP tested on 500 sample files. Ultimately, the system will cover up to 35,000 variants. But the most important part? The system works on the older machine – the one with a cutting cost of just 0.5 cents per part, compared to 1 cent on the modern equipment.
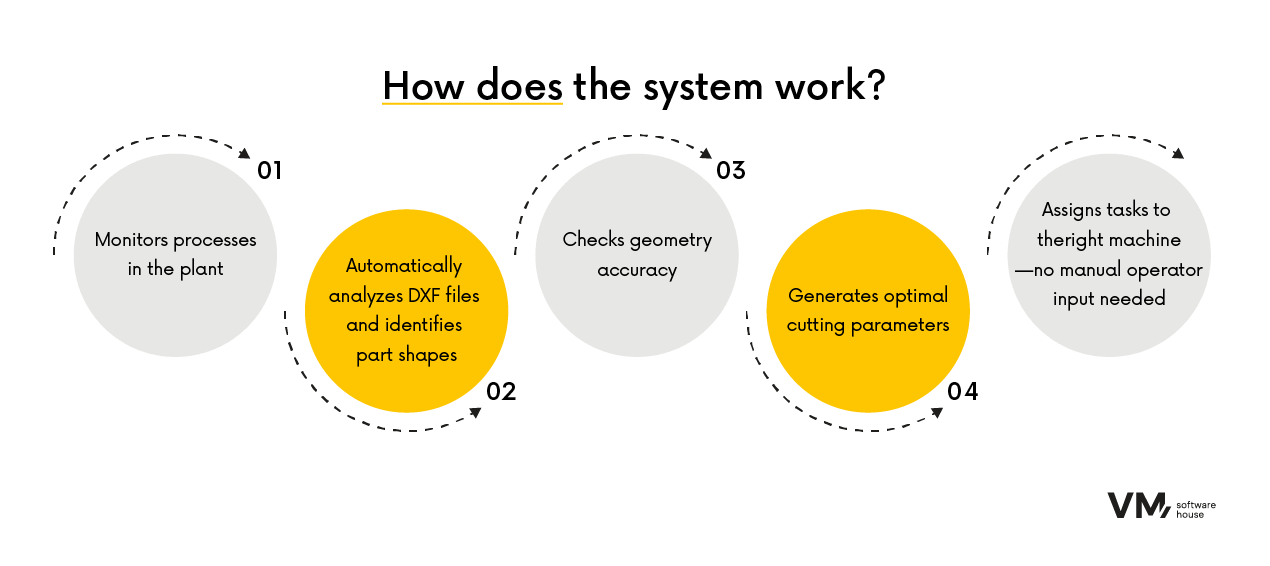
Outcome
Thanks to automation, a significant portion of production was shifted to the more cost-effective machine – without risk of errors and without requiring constant supervision by skilled operators.
The production process became:
- Much faster
- Less prone to mistakes and material waste
- More cost-efficient
- More environmentally friendly
- Easier to manage
By optimizing machine usage and better leveraging existing resources, the client gained measurable benefits:
- $25,000–$65,000 in annual savings (machine operation and maintenance)
- 4,800–6,300 kWh less energy consumed annually
- 1.9–2.5 tons of CO₂ emissions reduced annually
- Over 5 years, this translates to potential savings of up to $325,000 and a CO₂ reduction of 10–12 tons.
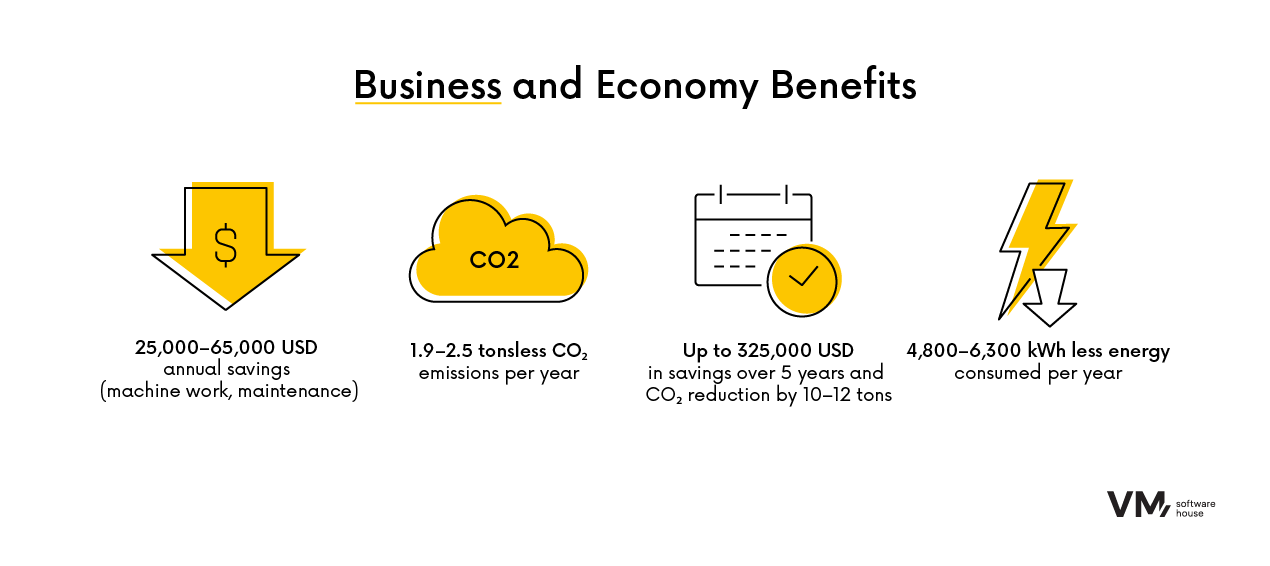
Collaboration Model
Data and Process Analysis
We mapped the entire process – from DXF file to machine settings. We identified exactly where losses occurred and how they could be automated.
Initial Model with High Potential
At first, the model recognized 500 shapes. That was enough to prove it worked. In later phases, the system is expected to cover the full database – up to 35,000 unique files.
Integration Without Equipment Replacement
We adapted the system to the existing older machine – no need to purchase new machinery.
Production-Environment Testing
The system was tested directly on the production line – using real files and under the factory’s actual working conditions.
Documentation and Ongoing Development
The client received complete documentation along with the tools and space needed to further scale the model independently.
Technologies
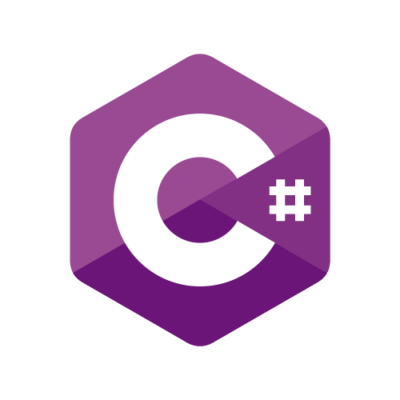
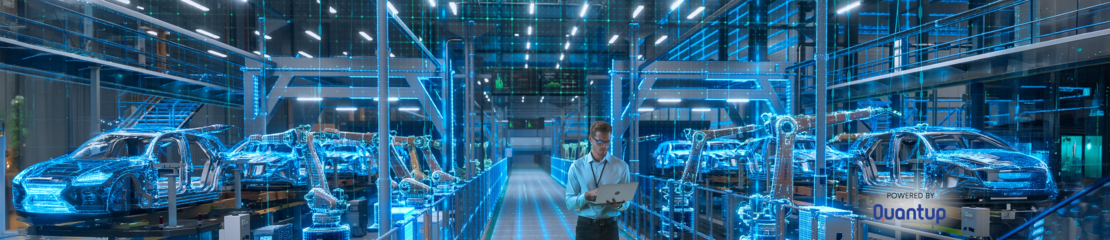
Help Desk for the Factory – Intelligent Maintenance Support Powered by AI and Shop Floor Expertise
Design, Development, DevOps or Cloud – which team do you need to speed up work on your projects?
Chat with your consultation partners to see if we are a good match.
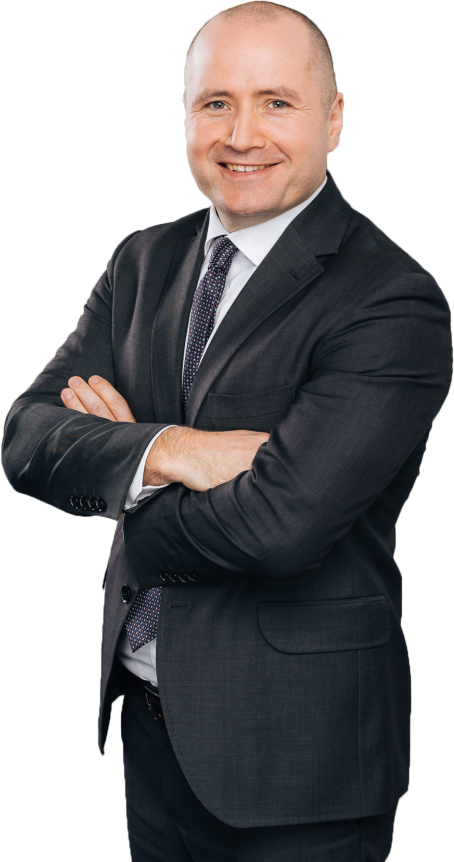